Get to Know about CNC Milling Coordinate System
CNC milling machines are used to create parts and components with complex geometries. In order to create these parts, the machine must be able to move in three dimensions. This is done by using CNC milling coordinate system, which helps the machine know where it is in space and how to get to the next point. In CNC milling, the coordinate system is the framework that defines the location of the tool and the workpiece. The three axes of the coordinate system, X, Y, and Z, correspond to the three axes of movement on the milling machine. The X and Y axes define the plane of the workpiece, while the Z axis defines the depth of cut. Needless to say, center coordinates of CNC machining are vital for every machinist and aspiring CNC operator to know. It is a fundamental part of understanding how these machines work. In this post, we will explore what CNC milling coordinate system is, how it works, and why it’s so important.
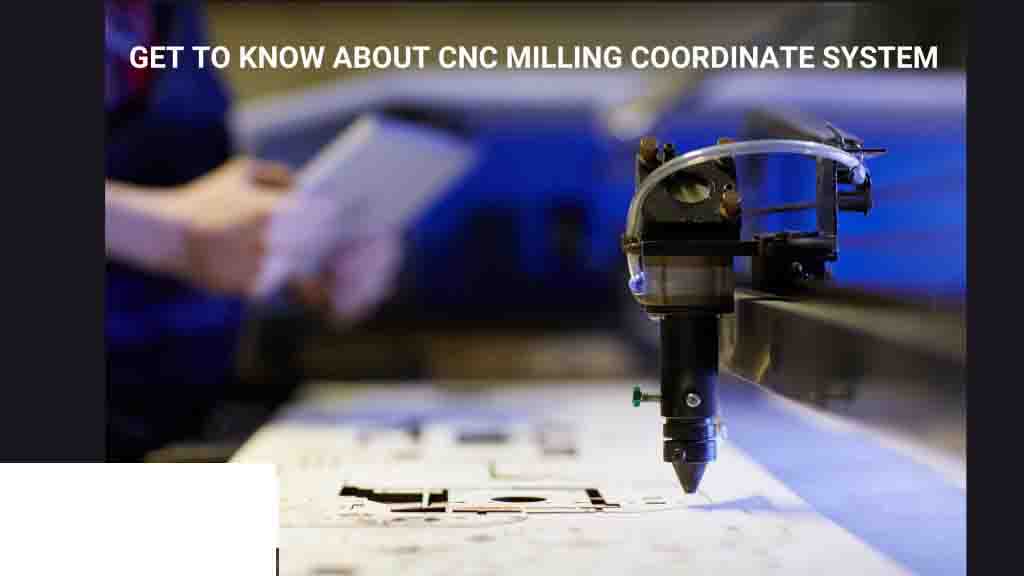
Why Do Coordinates Matter for CNC Milling?
Every CNC machine has its own coordinate system. In order to create an object, a CNC milling machine needs to know the coordinates of the points in space that make up the object. The CNC milling coordinates system is important because they help the machine know where to position the cutting tools as it mills the object. Without the coordinates, the machine would not be able to create the precise shapes and patterns. While the coordinates are critical for the CNC milling process, they are only one part of the equation. The machine also needs to know the size, shape, and feed rate of the cutting tools in order to create a successful milling operation.
Major Types of Center Coordinates of CNC Machining
In CNC machining, the workpiece is moved in relation to the cutting tool using a set of coordinates. These coordinates can be either Cartesian or Polar. The choice of CNC milling coordinate system is up to the operator and what they feel is the most effective way to control the machine.
- Cartesian Coordinate System: In CNC machining, the Cartesian coordinate system is used to control the motion of the cutting tool. This system uses three coordinates (X, Y, and Z) to define the position of the cutting tool. By inputting these coordinates into the CNC machine, the operator can control the precise movement of the tool. Cartesian coordinates are the most common type of coordinate system used. Cartesian coordinates are a system of coordinates that specifies each point uniquely in a plane by a set of numerical coordinates.
- Polar Coordinate System: Polar coordinates are a bit more complicated than Cartesian coordinates, but they offer some advantages, especially when working with curved surfaces. In polar coordinates, the workpiece is moved in relation to the cutting tool along a radius and an angle. This makes it possible to create more complex shapes and curves. Polar coordinates are often used in CNC machining because they can help to create more accurate and precise results. When using this system, the machine is able to move the cutting tool in a more consistent and controlled manner. This results in better cutting accuracy and efficiency, which is why polar coordinates are so popular in the world of CNC machining.
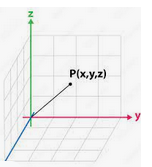
How a CNC Machine Uses Coordinates?
CNC machines work by reading a set of coordinates that tells the machine where to cut or shape the material. The coordinates are fed into the machine via a computer program. The machine then uses a cutting tool to follow the coordinates and create the desired shape.
The selection of the right center coordinates of CNC machining is critical in order to produce the desired results. The machine needs to be properly calibrated to the chosen coordinate system in order to produce accurate cuts. If the wrong coordinate system is used, the machine will not produce the desired results.
If you are not sure which CNC milling coordinate system to use for your next project, talk to your CNC machinist. Leading CNC machining service providers like China CNC Machining have the experience and expertise to help you choose the best coordinate system for the job. They will take into account the specific requirements of your project and recommend the best center coordinates of CNC machining for you.