A Detailed Discussion on CNC Milling of Curved Surfaces
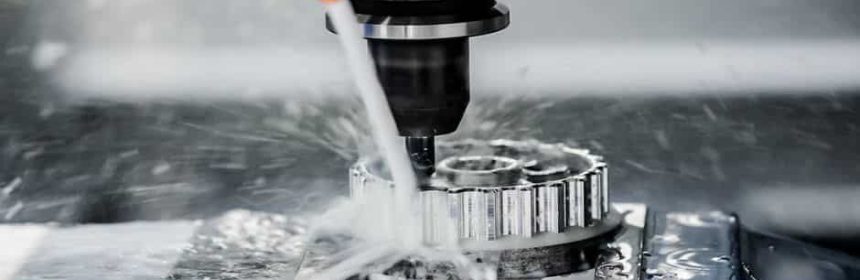
CNC milling is a process of machining irregular or curved profiles in various degrees. This type of milling falls under contour milling or form milling and is usually employed to build customized parts. Although this process is automated, it requires expertise in principles and programming to get it right over curved surfaces. CNC milling of curved surfaces requires elaborate preparations and several considerations. Are you intrigued to know how this process works and what steps are involved? This post discusses different aspects of CNC milling of curved surfaces.
Common Contour Milling Applications
Before going into the details of CNC milling of curved surfaces, you need to understand some applications of CNC milling of curved surfaces:
- Ball nuts
- Rotary Recesses
- Neck Ring Molds
- Threads
Important Tools Used in CNC Milling of Curved Surfaces
Generally, round end mills are used for contour milling curved surfaces. The following are a few common types of endmills used for the purpose.
- Ball Endmills: These endmills are also known as ball noses and possess a round cutting surface. They are generally used to mill contoured surfaces and are used for surface finishing applications. Ball endmills are known to produce brilliant surface finishes.
- Radius Endmills: These endmills feature a rounded corner to cut a workpiece in a specified radius.
- Insert-type Endmills with Rounded Inserts: The tools feature large tooling diameters and assure excellent productivity and great stability. Insert type endmills with rounded inserts are used for roughing operations.
Processes Involved in CNC Milling of Curved Surfaces
CNC milling of curved surfaces involves several steps. The following are a few common ones among them.
- Roughing: This is the first stage of CNC milling, where the workpiece is cut into a desired profile or shape.
- Semi-Finishing: The cut workpiece is machined as per the dimensional requirements. These parts may be further finished to achieve a particular surface finish.
- Finishing: In this step, any surface imperfections are removed carefully. The part is made clear of burrs and other imperfections. The final appearance of the part depends on the machining in this step. Thus, it is always performed using high-speed tools. In short, this process helps improve the aesthetic appeal of a workpiece.
- Superfinishing: Most standard parts may require no superfinishing. This is often done to produce parts with a smooth profile. Many applications in the medical industry require parts with high surface finishes, which is achieved through superfinishing. High precision and high speed tools are used to achieve the right type of super finish on parts.
How is CNC Milling of Curved Surfaces Performed?
CNC milling of curved surfaces involves several considerations. Once, you nail them, then the process becomes easy.
- Analyze the type of contour milling required. You may need parts with high surface finishes or standard surface finishes. In the latter case, high degree of precision and tooling may be needed. So, address the type of contour milling required.
- Address the risks involved in the milling process. For this, you need to address the following aspects.
- Depth of Cavity in Part Designs: Although part cavities may look impressive to users, they are unaware of the efforts that go in perfecting it. Right cutting tool and gauge length is needed to perform cavity depths in parts.
- Right Clamping Method: You need to determine the duration of time the workpiece will be clamped. This will help you prepare the right fixtures as per the requirement.
- Choose Proper Tool Holders: What if the workpiece rotates or vibrates on its axis during milling? The results can be disastrous. So, you need to choose the tool holders carefully. Pull studs, end mill holders, and ER collect chucks are some popular endmill holders used today. These tool holders are available in various dimensions. You can choose the right one based on the tool length.
- Material Cuts: You need to determine how much material will be cut from the workpiece. This will also help you evaluate some additional procedures, which will be required for semi-finishing and semi-roughing.
- Set the Correct Speeds and Feeds: The tool speed and feed can be set up depending on the amount of material to be cut from the workpiece. The feed rate depends on several factors, such as the type of tool used, the cut depth, the required accuracy, the material to be cut, and so on.
How to Minimize Vibrations during CNC Milling of Curved Surfaces
Although CNC milling of curved surfaces is a controlled process, vibration is one of the concerns for most CNC machinists. This vibration may be induced by various factors including the type of tool, hardness of the material, machine spindle errors, and so on. Here are some steps to minimize vibrations:
- Set the CNC machine on a solid floor with no cracks, seams, or discontinuities.
- Choose a CNC milling machine equipped with a vertical machining center or a ball screw. This will help reduce chatter vibration that generally occurs during CNC milling.
- Select the appropriate cutting depth or use a constant meshing tool path to avoid chatter vibration.
- Ensure there are no long overhangs on the end of your endmills while roughing rather, you can use extension tool holders or extension bars for the purpose.
- Use the right work holding fixtures, which would help ensure proper balance and grip during the cutting, because if the part is not properly secured, it will cause tremors and vibrations.
- Do not perform aggressive cuts on hard metals, as it can affect the material finishes.
If you have considering CNC machining services specializing in CNC milling of curved surfaces, you can consider China CNC Machining. The company offers precision CNC machining services and specializes in plastics machining. The experts at the company work with a wide range of plastics, including phenolics, PTFE, polyethylene, Delrin PEEK, and ABS to machine a wide range of regular or standard to close tolerance parts. China CNC Machining considers some of the OEMs in telecommunications, construction, electronics, material handling, food processing, fluid power, and energy as its biggest clients. You can get in touch with the experts at the company today to discuss your contour CNC milling requirements.