What you Need to Know about Plastic Burrs and Deburring – Part I
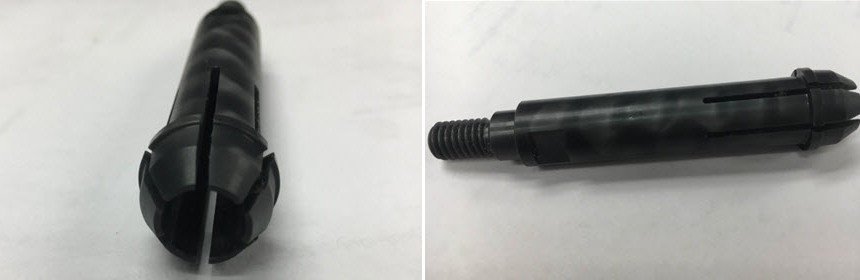
Burr formation is a common and significant problem in plastic component manufacturing. If not removed, burrs can be responsible for component breakdowns. For this reason, many companies use a variety of techniques for burr removal. In this post, we are talking about all things burr-related.
What is a Burr?
Also known as a flash, a burr is a small piece of material, or a raised edge, which has been left after the component manufacturing process. A burr can get created in different materials, including plastic, metal, and rubber. Besides component breakdowns, burrs can also give the part an unfinished, and disheveled appearance.
What are the Different Types of Burrs?
Machining operations can create four different types of burrs.
- Roll-over Burr: This is the most common type of burr. It basically looks like a bent chip, and can be of a large size. Roll-over burrs are also called exit burrs, as they are usually found at the edge of a cut.
- Tear Burr: As the name suggests, this burr is created when a piece of the material tears loose, rather than getting sheared off.
- Cut-off Burr: This refers to a projection of material left during a cutting process. Cut-off burrs usually occur if the work piece falls from the stock before the cut has been completed.
- Poisson Burr: This burr type is found most on plastic work pieces. When a plastic material is compressed, it can have a tendency to bulge out from the sides. A Poisson burr is a result of the bulging. These burrs also result in complete material deformation.
With this knowledge, you can now move onto the various deburring processes. There are a variety of burr removal processes. These will be discussed in the following post.