Design for CNC Machined Parts: A Few Key Considerations
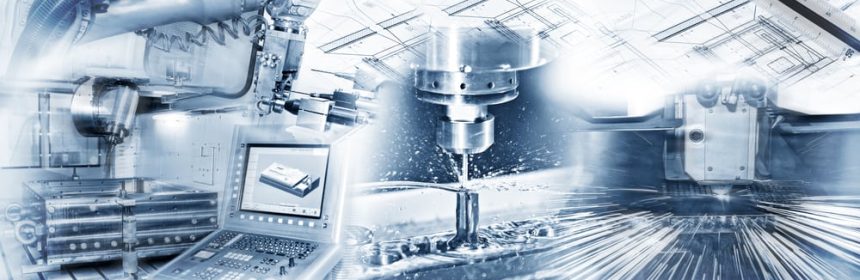
CNC machining is among the most popular manufacturing methods used today to create custom machined parts with optimum strength, high precision and tight tolerance. There has been a tremendous growth in the use of CNC machining technique over the years, owing to machining flexibility and its compatibility with several materials from wood and plastic to foam and metal. Although CNC machining is considered to be the fast and cost-efficient process to produce parts with high versatility, repeatability, and reliability, a poor design may produce adverse results. Hence, to get the most out of the CNC machining technique, it is imperative to pay utmost attention right from the start of the designing phase. Designers must adhere to several best practices to assure successful production of high-quality parts.This post lists a number of aspects to consider when creating design for CNC machined parts.
6 Golden Design Tips to Follow While Performing Design for CNC Machined Parts
There are several elements to consider in order to fully optimize designs for CNC machined parts. Sticking to such best practices helps to come up with high-quality and feasible designs, which in turn drastically reduces production times and costs associated with the process. Keep a careful note on the following design aspects.
- Cavities: Designers must keep the depth of any cavity at least four times its width. Considering this depth-to-width ratio is important, so as to avoid tool hanging, increased vibration, tool deflection, and tool fracture during the machining process.
- Thin Walls: The recommended thickness of CNC-machined part is 0.8 mm for metals and 1.5 mm for plastics. It has been noted that thin walls reduce the stiffness of the material, leading to increased vibrations. Parts with thin walls show tendency to chatter, which results in slow machining operations.
- Holes: Operators use either drill bits or end mill tools to drill holes during the machining process. Hence, designers must be careful while deciding the diameters of the holes. They should ensure to keep the drilling depth low to avoid machining complexities in the later stages. Do not create designs that require flat-bottomed holes unless necessary as this demands heavy machining.
- Tight tolerances: Assigning tight tolerances only to some critical features benefit the overall process in terms of speed and cost. This should be one of the critical elements to consider while creating the design for CNC machined parts as more features with tight tolerances increase the complexity of part production.
- Intricate Detailing and Features: Most CNC machining shops are equipped with machines that are capable to machine cavities and holes below 2.5 mm (0.1″) in diameter. However, when the diameter comes below to this, it would be challenging for the operators to machine them using the existing machines. Such scenarios demand micro-machining, which in turn requires specialized machines and expertise. Hence, it is recommended to avoid such design for CNC machined parts unless absolute necessary.
- Text or other Engravings: Although adding text or other engravings like part code or logo adds to the brand image, the process certainly adds to the cost. Hence, the decision on adding text must be made after careful consideration of hidden costs involved. In case adding texts or engravings is a vital requirement, then designers must consider using recessed text, which is cheaper to machine than its counterpart raised text.
Other than the points discussed aforementioned, keep a note on the following design considerations when it comes to CNC machined parts.
- Round the internal corners
- Limit the thread length
- Add radii when designing internal edges
- Avoid designing unnecessary aesthetic features
- Split up complex parts for easy and fast machining
- Limit the size of the parts as per the available CNC machines
Considering several aspects of a design like the ones aforementioned certainly helps produce precise parts cost-effectively without additional machining. Having an immaculate design as per the specifications leads to perfect prototypes and, ultimately, better end-use products. Any neglecting approach at the design stage would create inferior end products. This in turn delays the project and increases overall production costs. To avoid all these, it is recommended to partner with prominent CNC machining service providers in the market like China CNC Machining, who monitors all aspects like tolerances, RPM, and dimensions carefully during the design stage. Associate with such experts and get your design transforms to high-performing parts and products.
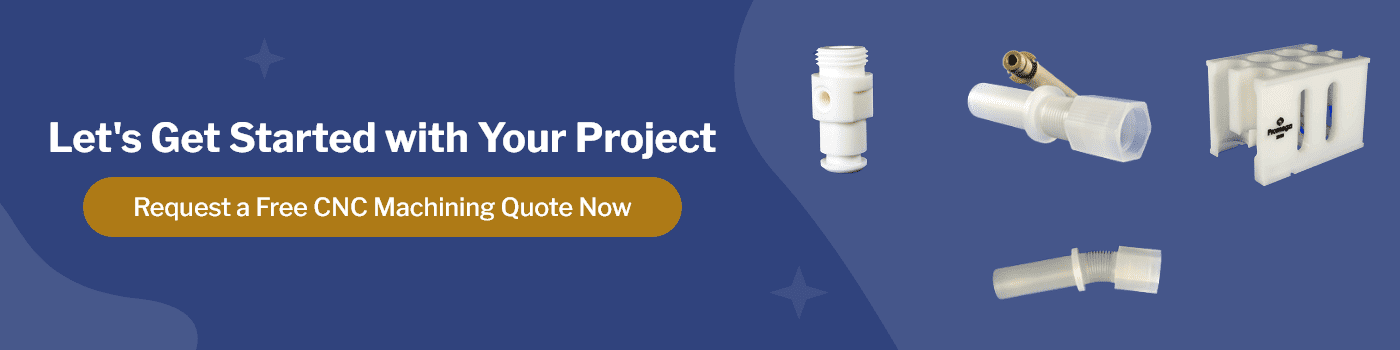